- The textile industry achieved a stable start in the first quarter of 2025!
- Summer is the perfect time for production! Hangzhou Yujie Chemical's non-woven fabric color masterbatch adds luster to many industries!
- Summer is the perfect time for production! Hangzhou Yujie Chemical's non-woven fabric color masterbatch adds luster to many industries!
- The textile industry achieved a stable start in the first quarter of 2025!
- Why choose Yujie nonwoven fabric masterbatch?
- The development prospects of the textile industry in 2025!
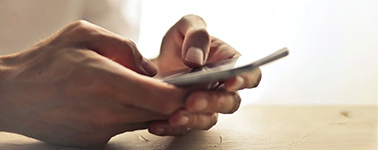
- Tel: 0086-13957173655
- Email: zpl620504@163.com
- Add: Canghexia No. 36, Tiyuchang Road, Xiacheng District, Hangzhou, Zhejiang, China
In today's world of plastic materials and products applied to all walks of life have been involved in all aspects, as well as every family, more and more enterprises to participate in the production and sales of plastic products in the past. Plastic products for the selection of the coloring has become a concern for the plastic industry issues. Today we look at Jill with relevant knowledge in this area!
1. Types of plastic colorants
Type of plastic colorants, its physical form is divided into four categories: Toner - powdered colorant; paste - paste colorants; liquid colorant; masterbatch - solid state colorant. Wherein, widely used is a powdery colorant and as a solid colorant. That toner in masterbatch.
2. Features of the colorants
Dye coloring characteristics
Directly add the appropriate amount of powdered aid of a method for coloring plastic particles with toner (pigments or dyes), also known as dry coloring.
Pros: good dispersion, low cost, small-batch operation. Because it obviates the other colorants, such as processing of human and material resources consumed masterbatch, paste, and thus lower cost, without limits on the amount of buyers and sellers. Masterbatch manufacturer can not do 1 ~ 2kg, but the quality of the toner can be specified as required, preparation is very convenient. Use dye coloring, compared with other granulated coloring resin processed experience a less degradation process helps to reduce the aging of plastic products, to increase its service life.
Cons: pigment in the transport, storage, weighing, mixing process will flying, pollution, seriously affecting the work environment. As environmental, business and other requirements of ISO 9000 index, dye coloring increasingly been limited, but the special effects for the coloring, using colored toner mixed directly with a number of colored masterbatch reach results.
For example: Some poor heat resistance, fear shear pigment powder made masterbatch, which withstand high temperatures due to the long time, and for a long time by the shearing action in masterbatch processing equipment, the coloring effect will be significantly reduced, as pearlescent pigments, phosphor, luminous powder. Toner is made with pearl colored plastic masterbatch then compared directly mixed plastics coloring pearl powder, pearl effect its going to weaken by about 10%, and injection molded products are also prone to flow linear scar and seams. We in the manufacture of this type of masterbatch, are taking appropriate measures to minimize the masterbatch in the process of heating temperature, time and extent of the cut (no twin-screw granulation machine, but with a single screw granulator etc.).
Dry coloring gives users another headache extruder hopper is easy to clean. For the colored toner in the role of white oil humectant, buildup on the inner wall of the cylinder (or even the screw). When you need refueling, cleaning the barrel became the site operator's problem, time-consuming material, less effective, and the use of colored masterbatch do not have this problem.
Further, the use of dye coloring, due to the need to evenly distributed pigment powder colored resin, so its good dispersion, this conclusion only for injection products, in particular thick-walled products, for blown film, spun products is another matter. Since toner generally been no pretreatment, when mixed with the resin after it alone from the extruder feed opening, screw, to spout such a distance in such a short plasticizing and mixing time, to make pigment powder the pigment molecules and the molecules are colored nicely hand in hand - fully integrated, can never be fully guaranteed, there will be "cooked" phenomenon. But this "cooked" phenomenon in the thick of products will be masked out, blown film, spinning products is obvious. Therefore, the latter method is still colored masterbatch based.
In addition, because of the different manufacturers of toner production date, batch number, the same brand of toner there are a certain color, even if you insist on using the same formula, but in the process is very difficult to batch to batch injection product color consistency, while masterbatch in the production process by way of sampling, testing, adjustment to compensate for each batch of toner color, contrast, color masterbatch for repeatability was superior toner.
Because toner for coloring plastics have various limitations, has been challenged other colorants, but because of the relatively low cost of production, fixed color, color is not limited capacity for SMEs in developing countries, the private sector who, in order to participate in the fierce market competition, the use of toner has its economy, especially in some kind of single-color, large output, less demanding coloring products, such as PVC windows and doors, EVA soles, or favor it therefore can not be completely out of toner colorants stage.
Features colored masterbatch
In order to overcome the drawbacks colored toner and improve the quality of plastic products, with the continuous development of the plastics industry, innovative types of plastic resins, additives types of plastics processing equipment and technology, a breakthrough, another way plastics coloring - - colored masterbatch has been widely adopted, masterbatch and coloring techniques are applied in practice continue to improve.
The so-called masterbatch, i.e. a process with the use of appropriate equipment, under the action of the adjuvant, the pigment (or dye) into the carrier by heating, plasticizing, mixing, shearing, and finally to a pigment powder with a carrier molecule molecular resin fully integrated, and then made with the resin particles of similar size particles. We call this a high concentration of colorants called masterbatch, its role and "saccharine" similar use, simply add the resin to be colored in a smaller proportion (1% to 4%), we can achieve coloring the purpose of the resin.
Compared with dye coloring, colored masterbatch has the following significant advantages:
(1) improved as a result of environmental pollution caused by toner flying problem, use the process easy to change color, do not have any special extruder hopper cleaning conveniently.
(2) targeted, color correct. Because masterbatch manufacturing facility in the manufacturing process has been applicable for performance resin, a reasonable choice of pigment (dye), additives, processing equipment, processing technology, the production process of different batches may bring color toner, timely correction, fill color, and then tested at the factory, so you can ensure the same grade masterbatch, before the two groups remained relatively stable color.
(3) Compared with the bulk resin stain dry granulation and then to make plastic parts, plastic products can reduce the use of masterbatch resin properties by the second post-processing caused by aging, will help improve the service life of plastic products.
Advantage of using a masterbatch is greatest: in the process, the role of the pigment in the additives, and kneading the masterbatch carrier resin after full fully integrated. When in use, by a certain percentage to be processed into the resin, masterbatch quickly into the role, and the resin is considered "relatives." Affinity - Compatibility significantly better than the dye coloring, therefore, for the production of films and spinning products manufacturers, better understand.
Masterbatch coloring has its limitations, due to add less, plastics processing time is short, the extruder screw length limit by, masterbatch dispersion often inferior to the toner. More than once the manufacturing process, the cost is certainly higher than the staining dye coloring. When the masterbatch carrier performance and demand differences colored resin, plastic surface often occur undispersed point, stain, pattern. Therefore, the use of masterbatch for its compatibility and dispersion rather limited.
Hangzhou Yujie Chemical Co., Ltd. Main masterbatches, pre disperse dyes, masterbatches and other products, such as our products are interested, please call our hotline: 86-571-85095115!
- Summer is the perfect time for production! Hangzhou Yujie Chemical's non-woven fabric colo
- The textile industry achieved a stable start in the first quarter of 2025!
- Summer is the perfect time for production! Hangzhou Yujie Chemical's non-woven fabric colo
- The textile industry achieved a stable start in the first quarter of 2025!
- Why choose Yujie nonwoven fabric masterbatch?
- The development prospects of the textile industry in 2025!
- Salute to the workers who have weathered the storms together | Yujie wishes everyone a hap
- Focus on the Frontier, Lead the Future with Wisdom | The 25th Masterbatch Innovation Techn
- Yujie Color Masterbatch: Add vibrant colors to your products!
- The "Danger" and "Opportunity" of the US tariff Escalation in the Textile Industry