- The textile industry achieved a stable start in the first quarter of 2025!
- Summer is the perfect time for production! Hangzhou Yujie Chemical's non-woven fabric color masterbatch adds luster to many industries!
- Summer is the perfect time for production! Hangzhou Yujie Chemical's non-woven fabric color masterbatch adds luster to many industries!
- The textile industry achieved a stable start in the first quarter of 2025!
- Why choose Yujie nonwoven fabric masterbatch?
- The development prospects of the textile industry in 2025!
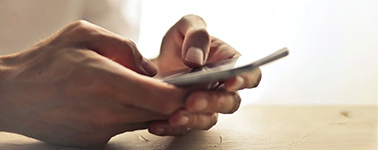
- Tel: 0086-13957173655
- Email: zpl620504@163.com
- Add: Canghexia No. 36, Tiyuchang Road, Xiacheng District, Hangzhou, Zhejiang, China
Plastic masterbatch use common problems and solutions
Masterbatch manufacturers: masterbatch very simple to use, just press a certain ratio and plastic resin mixed, with a variety of plastics processing requirements, extrusion can be.
Note that the color conversion, the hopper must be cleaned, with a primary or a plastic screw cleaning agent added in the machine rinse residual material cartridge, replacement of the filter, more preferably a 100 mesh filter; attention to the temperature is correct, and prevent color change.
Problems and treatment methods colored plastic products generally occur when:
1 product surface seeding:
The main reason:
① barrel and die with impurities;
② temperature is not correct;
③ raw material is heated too long residence time in the barrel;
④ masterbatch or toner dispersion untreated good;
⑤ filter has been perforated.
Treatment:
The presses the temperature to below the normal temperature 10-20 ℃, start the presses, plastic resin with color re slowest speed cleanup work, if necessary, to die apart to clean and adjust the temperature, the timely replacement of the filter . Use well-dispersed masterbatch or toner re-commissioning.
2 diffusion uneven:
The main reason:
① mixing uneven;
② temperature inappropriate;
③ masterbatch and materials compatibility poor;
④ presses itself plasticizing effect is poor;
⑤ masterbatch put the ratio is too small.
Treatment: stir, temperature adjustment appropriate replacement masterbatch or raw materials, replacement of other machine production, adjusted masterbatch delivery ratio.
3 often feed off:
The main reason:
① temperature is not correct;
② raw affinity difference;
③ masterbatch dispersion bad;
④ masterbatch delivery ratio is too high.
Approach: The more accurate temperature adjustment, replacement of materials used, replacement dispersed excellent masterbatch, masterbatch use lower proportion.
4 color variations:
The main reason:
① background inconsistent use of raw materials;
② presses are not clean;
Or the temperature of the toner low level ③ masterbatch used, the temperature is too high when the decoloring;
④ cutting the door is not clean;
⑤ process change;
⑥ color masterbatch or toner itself;
⑦ outlet material mismatches;
⑧ not clean blender or mixing time is not good control.
Approach: the use of color is consistent with the playing board and adjust the mix ratio of raw material good outlet; the presses, cutting doors and blenders thoroughly clean; switch to the proper temperature, consistent color masterbatch or toner ; using a stable process.
- Summer is the perfect time for production! Hangzhou Yujie Chemical's non-woven fabric colo
- The textile industry achieved a stable start in the first quarter of 2025!
- Summer is the perfect time for production! Hangzhou Yujie Chemical's non-woven fabric colo
- The textile industry achieved a stable start in the first quarter of 2025!
- Why choose Yujie nonwoven fabric masterbatch?
- The development prospects of the textile industry in 2025!
- Salute to the workers who have weathered the storms together | Yujie wishes everyone a hap
- Focus on the Frontier, Lead the Future with Wisdom | The 25th Masterbatch Innovation Techn
- Yujie Color Masterbatch: Add vibrant colors to your products!
- The "Danger" and "Opportunity" of the US tariff Escalation in the Textile Industry